Digital engineering and manufacturing describes the combination of digital capabilities and deep engineering and manufacturing expertise to design, develop, maintain and renew products, services and assets. It transforms traditional methods by utilizing advanced technologies such as digital twins, robotics, augmented and virtual reality (AR/VR), cloud computing, data analytics and artificial intelligence (AI).
Digital engineering includes a set of core digital processes and capabilities that form the backbone of intelligent products—such as data architecture, software design, engineering and development—to create products and services that are more personalized and intelligent.
Digital manufacturing is the application of advanced technologies to optimize and automate production processes. It’s the foundation for creating a highly efficient, resource-conscious and agile production to improve efficiency, reduce waste and shorten development time.
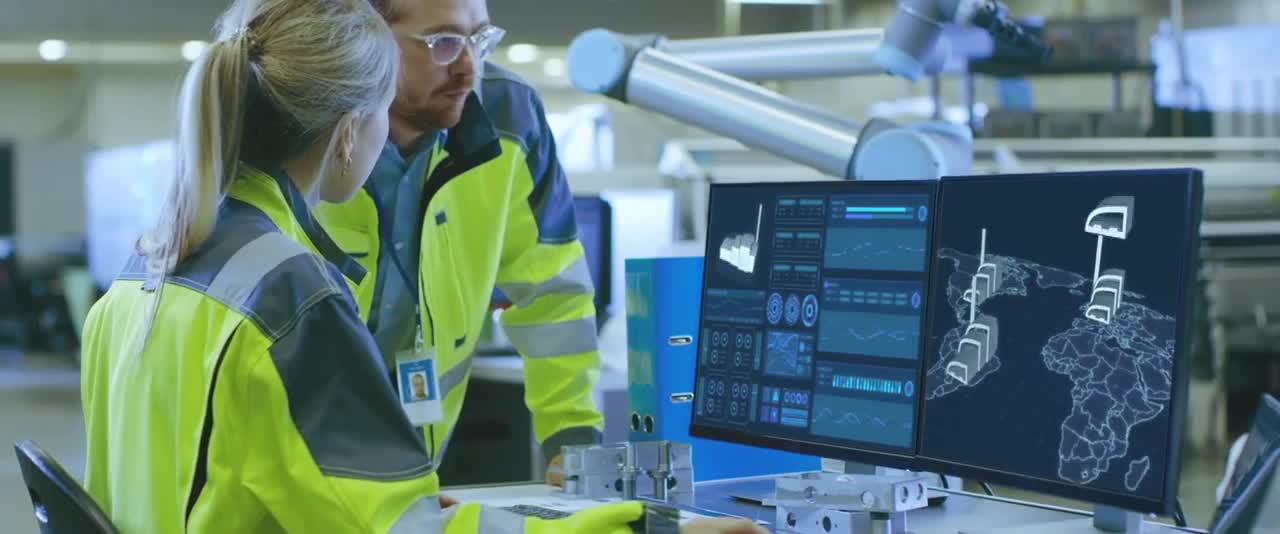
Why is digital engineering and manufacturing important?
In the rapidly evolving tech landscape, digital engineering and manufacturing are more than strategic choices—they're vital for enduring disruption and fostering adaptability. These practices offer a competitive edge in navigating ever-changing market dynamics. Moreover, digital manufacturing goes beyond efficiency gains. It also champions sustainability by reducing resource consumption to align with eco-conscious goals. Predictive maintenance through digital tools minimizes downtime and curbs raw material waste.
In this dynamic business landscape, fostering resilience and sustainability is paramount. Looking ahead, digital solutions will take center stage, commanding 43% of our investment focus in the coming three years, overshadowing reshoring and relocation at 29%, and plant site and warehouse automation at 21%. This strategic pivot, as seen in our "Resiliency in the Making" report, signifies the growing significance of digital transformation in our journey toward a more resilient and sustainable future.
What are the digital engineering and manufacturing advantages?
How does digital engineering and manufacturing work?
In essence, digital engineering and manufacturing is about utilizing a comprehensive suite of advanced technologies to transform how products, services and infrastructure projects are developed. For example, digital twins serve as a pivotal technology. These digital replicas of physical products or systems allow for real-time monitoring, analysis and simulation, ensuring that every facet of the design and manufacturing process is finely tuned for optimal performance and efficiency. Augmented reality (AR) and virtual reality (VR) technologies are seamlessly integrated into the product design lifecycle. Designers and engineers can visualize and interact with 3D models, facilitating collaborative design and decision-making, reducing errors and accelerating design iterations.
Cloud computing serves as the foundation, providing scalable storage and computing power for the massive data generated in the design and manufacturing processes. This enables seamless collaboration across distributed teams and facilitates real-time updates and access to critical information. Machine learning and artificial intelligence (AI) algorithms process this data to derive insights, optimize processes and make predictions, enabling data-driven decision-making, for example, for predictive maintenance. This is called a digital thread.
The integration of 5G connectivity ensures that real-time data exchange, even in highly complex and automated manufacturing and construction environments, is smooth and seamless, facilitating communication and coordination between various components of the development process. For example, autonomous robotics solutions bring automation and precision to manufacturing processes, reducing human error and enhancing overall efficiency.