Digitize what you make, revolutionize how you make it
Use data and AI to reinvent your engineering, manufacturing, infrastructure and capital projects. Drive more efficient and sustainable operations, greater productivity, customer relevance and growth.
Digital engineering & manufacturing now
$1B
Is the average investment companies will make in manufacturing and supply chain resiliency
68%
of companies plan to boost investments in multi-skilled workforce over 3 years to enhance agility
78%
of companies will use multiple manufacturing sites in 3 years’ time to boost flexibility, responsiveness and sustainability
$1.6T
is the potential revenue growth left on the table annually by companies, as engineering, supply, and production vulnerabilities are exposed by disruptions
Reinvent with digital engineering & manufacturing
Innovate at the pace of customer demand
Optimize your traditional R&D and engineering operations with data, AI and Cloud. Speed your time to market and meet ever-changing customer demands with data from digital threads and digital twins.
76%
Accelerate time to market
By gaining better visibility, and integrating and automating your processes, you can reduce your time to market.
Reduce R&D costs
Move from a traditional operating model to more modern engineering methodologies or an agile concept to reduce costs.
Reduce carbon emissions
Embed technology along the entire product lifecycle to reduce energy consumption.
Improve engineering efficiency
Free up your engineers to focus on high-value tasks by implementing automation and data digitization/AI analytics.
Improve product quality and service
Data insights and agile processes reduce issues with your products, process, and service quality.
Create customer loyalty
Data and customer insights help to develop customer-centric products and services that they love.
Use data and AI to reach end-to-end adaptive automation
Create your roadmap to end-to-end autonomous — and sustainable — operations by combining data, cloud and AI. Apply transformative technologies to make the factory of the future a reality.
$395BN
Maximize your production potential
Run two or three times more performance improvement initiatives every year and double the rate of improvement of your overall equipment effectiveness (OEE).
Improve end-to-end performance
Improve quality, reactivity, costs and sustainability, constantly managing the trade-offs and improving resilience.
Reach truly market-driven operations
Fully integrate manufacturing into your product lifecycle and supply chain, speeding your reaction to market demand and your time to market of new products and services.
Meet sustainability targets
Transparency across the product life cycle enables insights that help reduce the organization’s carbon footprint.
Bring your workforce along
New collaborative ways of working break functional silos, improve processes and enable human/machine balance for a safer and more satisfying worker experience.
Customer-first transformations boost incremental revenue
Customers increasingly demand personalized, connected products and services. Switch to platform-enabled physical products and platform services to unlock value and pivot to an as-a-service business.
76%
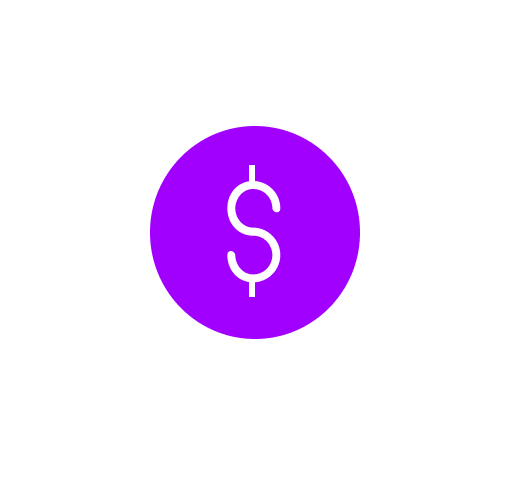
Expand revenue opportunities
Assess the maturity and capabilities of your current portfolio. Develop a vision and business strategy to meet the organizational goals through innovation.
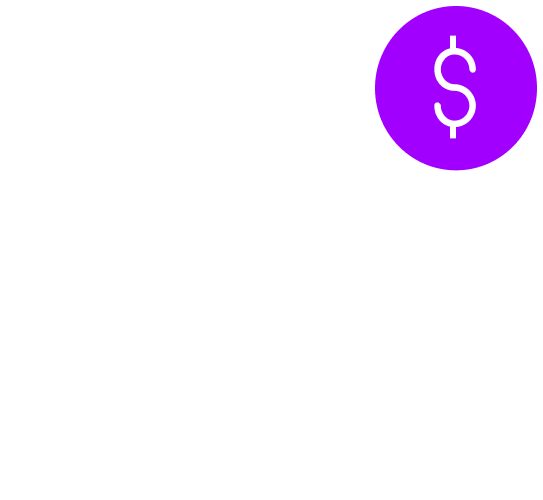
Speed your time to revenue
Accelerate the product design and development lifecycle by using the right technology and architecture to transform your organization.
Reduce lifetime R&D cost
Align your platform operating model with your business goal and strategy with an agile, platform-centric business model, talent organization and shared mindset.
Reduce platform development cost
Transition to modern engineering using cloud-native services (PaaS), product management approaches and composable thinking.
Improve ability to iterate
Effectively select and manage your ecosystem of platform tools and methodologies with a product lifecycle management rigor.
Increase service income
Use predictive maintenance, omnichannel support, connected worker technology and more to deliver superior service experiences to your “always connected” customers.
Future-proof product development
Scale up engineering services by using extended ecosystems to boost transformation and innovation.
Optimize your manufacturing and warehouse operations
Implement automation and robotics to advance human and machine collaboration — mitigating labor shortages and driving efficiency, sustainability and productivity.
68%
Address labor shortages
Robots collaborate with personnel to fill the void and meet demand.
Increase workforce productivity
Realign the workforce and add a fleet of smart robotic workcells to increase throughput while making operations efficient.
Deliver high-quality output
Smart robots use computer vision and machine learning to reduce errors, shifting human focus to complex problems and strategic initiatives.
Meet sustainability benchmarks
Smart robots continuously improve to reduce waste and energy, helping organizations reach their sustainability objectives.
Improve production resilience
Integrated smart robotic workcells use business and robot data to collaborate and dynamically operate, addressing variability in demand.
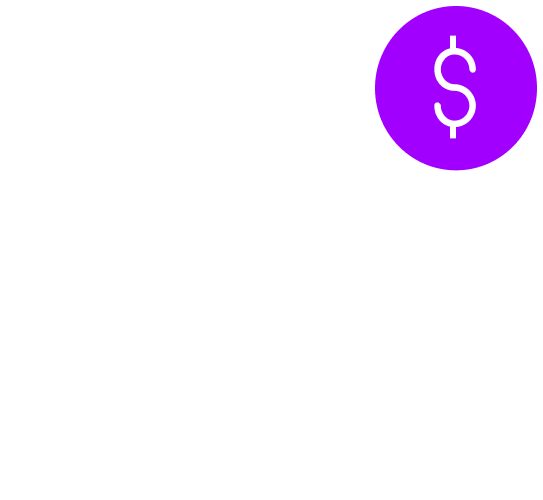
Make a financial impact
Achieve ROI faster with highly automated operations.
Mitigate asset-related risk with greater transparency
Transform your asset management using a holistic journey, moving from a reactive situation through to a preventative, predictive and eventually prescriptive approach.
1.8x
Increase in production throughput
Set up a strong foundation with an agile operating model. Then deploy standards for work management and asset lifecycle management.
Stronger asset utilization
Integrate your enterprise asset management and asset performance management systems to improve workflow, goal setting and asset performance.
Better asset performance
Improve your asset performance and decrease your risk of asset downtime by reducing breakdown and unplanned maintenance activities.
Improved labor productivity
Increase workforce efficiency and productivity when executing predictive, proactive and reactive work.
Less maintenance and repair
Balance your maintenance, repair and operations inventory by:
- Increasing capital efficiency
- Decreasing stockouts
- Reducing capital expenditure
Revenue and sustainability
Create long-lasting value by using the technology ecosystem to decarbonize your asset management value chain, reduce emissions, wastewater and leaks.
Intelligent aftermarket operations unlock value
Use managed services to operate, automate and transform processes with accelerators that enhance customer experience while creating greater efficiency — unlocking value from new revenue streams.
65%
Create new revenue streams
Build longer-term customer relationships through product upgrades and reliable servicing.
Improve product reliability
Real-time alerts reduce the time it takes to detect and contain emerging issues and to fix root-cause quality issues.
Grow customer loyalty
Improve product quality and remediation for higher customer satisfaction. Make aftersales repair and maintenance services invisible to the customer.
Increase service revenue profitability
Use data and digital technologies to reduce aftermarket operating and capital expenditures, including warranty cost and cost-of-poor-quality goods (COPQ) . Increase aftermarket workforce productivity.
Improve service operations
Use IoT and advanced robotics for remote and predictive maintenance. Monitor connected products in real time. Digitally manage warranty claims.
Reinvent capital project delivery
Combine the power of data, technology and people, with sustainability at the core, to deliver the projects of the future on time and budget.
13%
Improved capital efficiency
Expertise across funding, financing and capital deployment optimize the project cost, operating model and delivery approach.
Meet milestones and deadlines
Project managers and digital project management tools deliver a more efficient portfolio, program, project analysis and closer schedule control.
Increased on-site efficiency
Enable real-time monitoring of workers and assets to increase field productivity and time on productive zones.
Improved project safety and worker experience
Construction management connects manpower materials and machinery in real time to provide visibility where it matters most.
Enhanced supply-chain effectiveness
Boost supply chain efficiency by improving:
- procurement spend
- supplier relationships
- logistics and transportation efficiency
- inventory levels
Decreased carbon
Achieve your goals for sustainability and GHG emissions by using technology to embed sustainability in your strategy.
Reduced time to start up
Refine your execution plan and operational readiness support to reduce time to start up.
Areas we support
What’s trending with digital engineering and manufacturing
Awards and recognition
Accenture named a leader in smart manufacturing
Accenture is positioned as a leader across three recently published IDC MarketScape reports. According to the recent reports, “Customers appreciated Accenture's vast knowledge and expertise, its global network of skilled professionals, and its ability to manage complex projects from start to finish, while keeping the big picture in mind.”
A Leader in Generative AI Engineering Services
Accenture is positioned as a leader in the Zinnov Zones ER&D and Digital Engineering Services Ratings 2023. According to the report, the acquisitions of Objectivity and Flutura have expanded Accenture's cloud, analytics and AI capabilities, enabling the development of innovative solutions. A standout achievement is Accenture's launch of a 1,600-person Generative AI and Large Language Model Center of Excellence (COE), exemplifying their commitment to innovation.
A leader in digital engineering services
Our leaders
Nigel Stacey
Global Lead – Industry X
Fay Cranmer
Senior Managing Director – Industry X, Growth Markets Lead
Aaron Saint
Senior Managing Director – Industry X, North America Lead
Götz Erhardt
Senior Managing Director – Industry X, Europe Lead